Thermal Management Part 1: How Hot Is Too Hot?
By Steve Somers, Vice President of Engineering
Thinking about the topic of thermal management brought back memories of old round table discussions at college with an old ham radio buddy named Don. Don found it quite challenging to build radio transmitters from scratch; but, not the regular types of projects you would see in do-it-yourself articles. In what I would call an artful way, Don really "pushed the state of the art".
Clutching a cup of that vending machine coffee in the student lounge and listening intently to Don's experience building a 400 watt transmitter using five 6AG7's mounted to the underside of a large coffee can lid which submersed those tubes upside down into a reservoir of water, was a riveting discussion for anyone in engineering school. What's a 6AG7? It's a medium-sized, pentode, metal-can radio receiving tube with an octal (8 pins) base. Originally used as a video output amplifier in '50s era TV receivers, this tube is capable of only 10 watts plate dissipation. Don's ability to communicate with other hams was complicated by the need to replenish his coolant in real time using a small watering can kept nearby. Immersed to within one half inch of their base, these five tubes generated a constant column of steam.
Think about it. Would it be possible to leverage 400 watts or more from those five tubes? That's 800% of their collective power rating. Sure it is. The BIG question is: For how long? Theoretically, that much power could be delivered all day long if the heat can be efficiently transferred away from the crucial elements of the tubes. Efficiently (successfully?) moving potentially destructive heat away from systems doing work is called thermal management.
Getting Into Management
Thermal management is all around us in destructive and non-destructive forms. All objects or systems will, via fundamental physical laws of our environment, attempt to equalize their operating temperature condition with their surroundings. Warmer objects are said to give up, or transfer, heat to the colder objects. Over time, without additional work applied, all objects within a system will ideally approach the same temperature; thus, attaining a state of thermal equilibrium. Take a few moments to read the sidebar called Thermo 101.
Whether the internal heat rise of an object is self-destructive depends on the rate at which excess heat is transferred away to its surroundings. Remember from Thermo 101: Energy flows from warmer bodies to colder bodies. The transfer of molecular energy to a colder body is the process of equilibrium attainment. In electronic design terms, we call it a heat sink since heat is absorbed, or "sinks into" the colder body. Eventually, both bodies in close relative contact will attain the same temperature as long as no additional energy is input to the system.
Paying Twice
Heat rise in electronic equipment directly affects product reliability. All electronic components contain a "system" of heat production and transfer. Passing electrons rapidly through circuitry to do work causes many particle collisions. Heat rise is inevitable. Within each component are features that draw or transfer the heat rise to ancillary structures. The efficiency of heat transfer internally is limited by physical features and materials.
You might say that we potentially "pay twice" for any system. We pay at the front end in the form of dollars for the power to run the system. We pay again at the back end when temperature effects compromise the potential operational life span. Temperature rise has the highest impact on component life.
In our world of electronic product design, we live by this rule of thumb: For every 10 degrees Centigrade rise in temperature, the average reliability is decreased by 50 percent. Or, from the quality assurance department's point of view, if we can lower the temperature by 10 degrees, we'll double the reliability. In other words, we will double the expected life within any predictable failure rate. Another way to look at this, for those interested in buying products with good MTBF (meantime between failures) ratings, is that MTBF will, on average, double if the operating temperature is lowered 10 degrees.
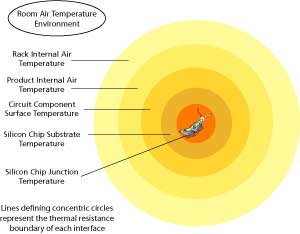
Figure 1: Thermal boundaries, or gradients, stack up to limit heat transfer from hot components to cooler environment's air. (High Resolution Image)
Cold is Relative
The concept of cold is relative. Anything feels cold if its temperature is lower than the contacting body. If the contacting body is transferring more energy than the cold body can sink away, the cold body will attain equilibrium with the warmer body and no longer be perceived as colder. In the opposite condition, the colder body will continue to feel cold. Cold bodies of sufficient mass can sink all available heat from a warmer body. Equilibrium will cause the warmer body to become the same temperature as the colder.
The rate at which heat transfer occurs between two bodies depends on the medium of contact in their environment. Solids, liquids, and gases have different rates of transfer, or thermal resistance. Thermal resistance may be thought of similarly to electrical resistance in a circuit. Resistors in a circuit have a corresponding voltage drop associated with a specific current flowing at a given time. Thermal resistance is a measure of how many degrees of temperature rise "drop" across the contact barrier between two bodies' contact surfaces. This measure of thermal resistance is commonly given in degrees centigrade per watt. (A direct comparison is not altogether straightforward. If you desire further insight, look up Reference 1 on the Internet.) There is a corresponding thermal resistance between the active heat source and each subsequent contacting body along the path to the external environment. Knowing the thermal resistance at each point of contact in a cooling system allows us to calculate how hot the active component, a silicon chip for example, will become in an application environment. See Figure 1 for a simplistic example of this "shell" concept. Figure 1 will be used in more detail in Part 2 of this article.
At the molecular level, the surface of most bodies is not very smooth. Points of intimate contact exist along with points separated by surrounding air, or other gas. Gases are good insulators and, therefore, have higher thermal resistance or lower thermal conductivity than most solids. Pressure and contact intimacy play a large role in the efficiency of heat transfer. This explains why thermal grease and mechanical fasteners have been the traditional assembly method for power semiconductors and heatsink materials.
Note the relative differences in thermal conductivity of materials in Table 1. It's no surprise that we use lots of aluminum for component heatsinking. Aluminum's conductivity is four orders of magnitude higher than air. Conversely, this accounts, in part, for the large surface areas needed with heatsinks (i.e. fins) since the number of gaseous molecules in contact with the aluminum heatsink at any moment is far less than the number of hot aluminum molecules ready to give up energy. Thermal conductivity tracks with the overall resistivity of materials. The relationships of aluminum, copper, silver, and gold parrot their relative properties as electrical conductors as well as heat conductors. With aluminum being easy to work and lower in cost than copper, it's the most practical choice.
We must move lots of air molecules to account for the relative inefficiency of air as a heat conductor. Looking diametrically at this attribute, we conclude that air, glass, concrete, and wood are good insulators.
Thermal Management at Extron
Thermo Thermal-Management Rule of Thumb #1: No component should be so hot as to preclude the indefinite placement of a human finger thereon. |
If I can just stand to indefinitely maintain finger touch on a component during its normal operation at room temperature, it is typically no hotter than about 45°C (113°F) and likely to be reliable. I have given products the finger test for years and it has served me well. Occasionally, I'll walk by an engineer's bench and, if we discuss temperature rise issues of a project, I first feel around the operating circuit using my index finger beginning with all the active components, then resistors, then capacitors, etc. For more "resolution", I use my little finger since it's less calloused and more sensitive. When I can maintain touch on all components, the circuit design is less likely to develop general temperature-related failures. Of course, cooler temperature sensation is better.
This rule of thumb is for components operating in free air. What happens after the enclosure is applied? This leads to decisions on product environmental operating temperatures. In the future, look carefully at the manufacturer's specified maximum operating temperature environment. This specification dictates the maximum recommended air temperature that the product should experience when it has reached system equilibrium. Curiously, most products are specified for no higher than a range of about 40°C to 50°C (104° to 122°F).
Thermo Thermal-Management Rule of Thumb #2: A product's internal components shall not exceed their absolute maximum operating temperature when subjected to the agreed-upon product maximum environmental operating temperature. |
Common wisdom in electronic product design dictates that active components will have higher operating temperatures than their respective environment (unless, of course, you are building refrigerators). When this is not true, the system will fail due to over-temperature conditions. This thermal difference works to draw heat from the active components. In system design this concept is working at all levels from components on circuit boards to equipment components mounted in racks.
The specified maximum environmental operating temperature is intended to reflect the considerations for thermal stratification from environment to enclosure to component to package to chip to operating junction. And here we come to the all-important point – the junction temperature.
The junction in a component is that boundary where the concentration of electron activity is highest, thus creating the most heat generation at the molecular level while doing useful work. Every contact layer between the junction and the outside world adds cumulative thermal resistance, or temperature drop. From the outside looking in, higher environmental temperatures mean less heat per unit area per unit time conducts away from the junction. Beyond the maximum junction temperature, molecular interactions occur at such a rate to become self-destructive. Actual "melt-down" of the junction usually occurs.
|
When it comes to the study of heat, energy, and thermal issues, the fundamental laws governing heat transfer always come into play. I'm talking about the laws of thermodynamics, which characterize the study of energy. We know that energy exists in many forms and is used to bring about change or to perform useful work. Energy exists as heat, light, electrical energy, and chemical energy. Our understanding of energy transfer within our universe revolves around the concept of the "closed system". The first law of thermodynamics states that energy may be transferred or changed, but cannot be created or destroyed. This is often referred to as the conservation of energy and implies that the total amount of energy in the universe is constant and merely changes from one form to another. The second law pertains to heat energy transfer. With the closed system concept in mind, for any spontaneous process there will be an increase in entropy. Entropy is a measure of the amount of disorder in a system. Other equivalent ways to consider the second law are: a) heat flows only from a warm body to a colder body; b) not all heat may be converted to useful work; c) all isolated systems become disordered in time. The second law most notably applies in our understanding of heat engines and the direction of heat transfer. The third law describes the relationship of thermal motion and temperature as we measure it. When all thermal motion of molecules stops, a condition of absolute zero is attained. Absolute zero represents 0°Kelvin, or -273.15°C. The estimated temperature of empty space in the universe is about 2.7 Kelvin. Near the beginning of this article the concept of equilibrium is discussed. As it turns out, the concept of equilibrium implies a MOST fundamental law preceding the first law of thermodynamics. The concept is: If, at the same time, two systems are in thermal equilibrium with a third system then all three systems are in thermal equilibrium with each other. Being so fundamental, this concept has been coined as the "zeroth law of thermodynamics". |
Good practice involves deciding on useful design guidelines for successful management within the maximum junction temperature specification. For semiconductors, a common guideline is to remain within 80% of the maximum while operating the product within the maximum environmental temperature. Junction temperatures range typically from about 100°C to 150°C. The enclosure plus all other "junctions" encountered between the outside environment and the semiconductor's junction temperature present a complex design responsibility. Should the systems integrator not follow recommended product temperature guidelines, the remaining 20% temperature rise headroom may determine the difference between system success and failure.
As systems designers, you are most often confronted with a collection of products each of which has an energy requirement rated in watts of electricity. How do we determine how much heat will be produced within the immediate environment for that system of equipment? Let's start with an understanding of the relationship between the basic units used to quantify heat, power, and cooling.
BTUs, Watts, and Tons of Air
Determining heat loads, temperature rise, and cooling solutions fall within a realm of related, but different, units. Electronic equipment essentially takes all supplied power and converts it to heat. Power consumption (read: heat generation) in electronic equipment is normally stated in watts. Heat rise is typically stated in British Thermal Units per hour (BTUH). Cooling systems, such as air conditioners, may be rated in "tons" of cooling capacity, or in BTUH. Calculations for management of heat load situations can become complex. Within most industries, rules of thumb and typical value models for heat contribution are used to lighten the task of computation. Let's take a look at these important relationships.
Watts
One watt is equal to one ampere of electric current operating through one volt potential difference. One thousand watts used over one hour's time is one kilowatt-hour. Some good numbers to remember for use in conversion are:
- One watt-hour of electricity produces 3.412 BTUH.
- One ampere of electricity operating at 115 VAC generates nearly 400 BTUH.
- At 230 VAC, one ampere is generating twice that amount.
Usually we assume that our equipment is a pure resistive load and we use the stated wattage rating verbatim. Heavy equipment loads with inductive or capacitive components can cause a phase shift between voltage and current usage resulting in a lower power factor. The power factor, when less than 1, raises the apparent power requirements and must be factored into our total power calculation as it pertains to heat production.
British Thermal Unit
The BTU equates to the amount of energy (about 252 calories, 0.293 watt-hours, or 1,055 joules) required to raise one pound of water from 58.5 to 59.5 degrees Fahrenheit at standard pressure (30 inches of mercury). An item using one kilowatt-hour of electricity will generate 3412 BTU. You may find it interesting to look at Table 2, which lists the BTU content of many common energy sources.
![]() Table 2: BTU content of common energy sources (High Resolution Image) |
Tons of Air
I've often times thought the units of air conditioning capacity to be a peculiar concept. It happens to be one of those units derived from more primitive beginnings, that being melting ice. One ton of cooling capacity equals the amount of cooling provided by melting one ton (2,000 lbs.) of ice. Therefore, a 2-ton air conditioner does the same work as two tons of melting ice per hour. Air conditioner capacity may also be stated in BTU per hour, BTUH. One ton of cooling equals 12,000 BTUH. That typical two-ton system is equivalent to 24,000 BTUH.
We've looked at some definitions and imparted some of our rules of thumb for thermal management, which I hope you may find useful in the future. You may find that you have developed some of your own rules of thumb; or in the adverse case, maybe you've developed burnt thumbs. This article lays the foundation for additional discussion on the practical application side of thermal management that I will cover in Part 2…namely, considerations for installing equipment in small spaces and equipment racks. If I could conjecture about some rules of thumb my friend Don might have used for his water-cooled 400 watt transmitter, they would optimistically be: 1) be sure the water can is half full and, 2) be sure the 6AG7 cooling tank is never half empty.
References
- "Thermal Resistance: an oxymoron?" by Clemens Lasance, Philips Research Laboratories, source: http://www.electronics-cooling.com/Resources/EC_Articles/MAY97/article2.htm
- Conductive Heat Transfer from the Engineering Tool Box web site at: http://www.engineeringtoolbox.com/ 24_428.html
- Thermal equilibrium at http://hyperphysics.phy-astr.gsu.edu/hbase/thermo/thereq.html
- Laws of Thermodynamics at http://physicalgeography.net/fundamentals/6e.html
- Laws of Thermodynamics at http://www.emc.maricopa.edu/faculty/farabee/BIOBK/BioBookEner1.html